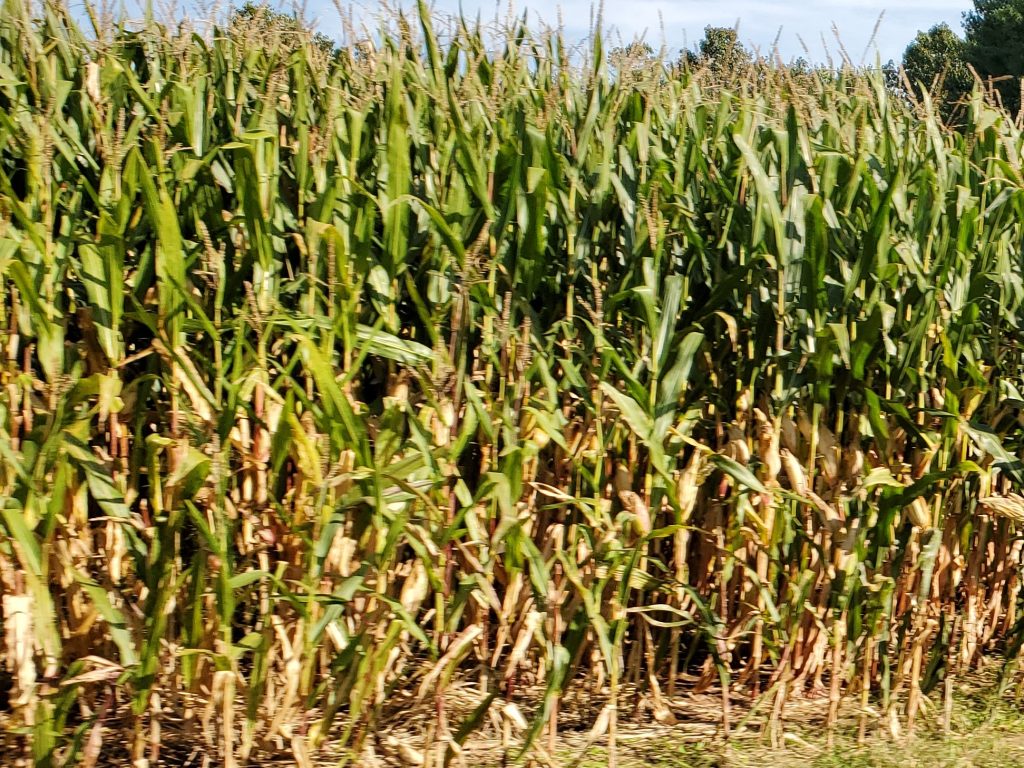
As technology and manufacturing become more intertwined, and definitions of words are reused in virtual senses we often times come to forget their original meaning, or why they have meaning or what the definitions are to begin with.
The idea of the term “Post Processing” is an interesting example. 25 years ago the idea of letting anyone seeing an uncured or unpost processed 3D model was enough to strike fear into the hearts of 3D Printer sales teams. Hardened sales reps would stay after hours at trade shows rooting through the trash of competitors for a model still in the “green state” while quietly disposing of their own printers’ unfinished model.
(The term green state is now similarly used to describe the fragile condition a metal part is in immediately prior to post processing.)
Post processing can literally include anything you might imagine that could or would change, add, or remove geometry. It could be sanding, curing, heating, cooling, drilling, tapping or boring to name a few. Some might be thought of as “best practices” while others are truly required depending on the method of 3D printing being used.
It is a catch-all phrase at an attempt to define when the manufacturing process ends on a 3D Printer. As with all beginnings and ends, it can be a difficult thing to define – yet it must also be certain. Likely to do the polished nature of assembly lines, costs associated with post processing has become integral to understanding ROI and potential pitfalls associated with logistics and subsequent disciplines between manufacturing and end user.
It can often be difficult to compare things that are not comparable – however that’s not to say it shouldn’t be attempted for the sake of advancement. There are still people who stand at the supermarket and shuck their own corn. But there are also people who will never ever shuck their own corn and will take it tightly wrapped in cellophane. Yet others may prefer it in a can. And still there are others who will find it completely ludicrous to “require” a machined heavy metal object (can opener) to access their food! Don’t tell that consumer that some can openers now require electricity.
Now there can be several takeaways from that thought experiment however the one we’re concerned with is learning to understand and gain access to as many of those consumers as possible. As the technology to create advances, so does the technology within households and businesses. This is a new beginning of providing customers with additional purchasing options based on the level of post processing required by the end user. The only printer available right now to anyone who wants to begin to unlock the potential of shifting post processing downline is the ETEC Xtreme 8K DLP from Desktop Metals.
Top-down digital light processing on the Xtreme 8K comes with the ability to produce strong, stable, and fully-isotropic parts suitable for demanding end-use applications.
Full range of breakthrough materials, including Henkel Adhesive Technologies Loctite® IND 405 and IND3843, as well as Adaptive3D Elastic ToughRubber™ are qualified on the Xtreme 8K.
Learn more about our material selections. https://bit.ly/3LARRR1